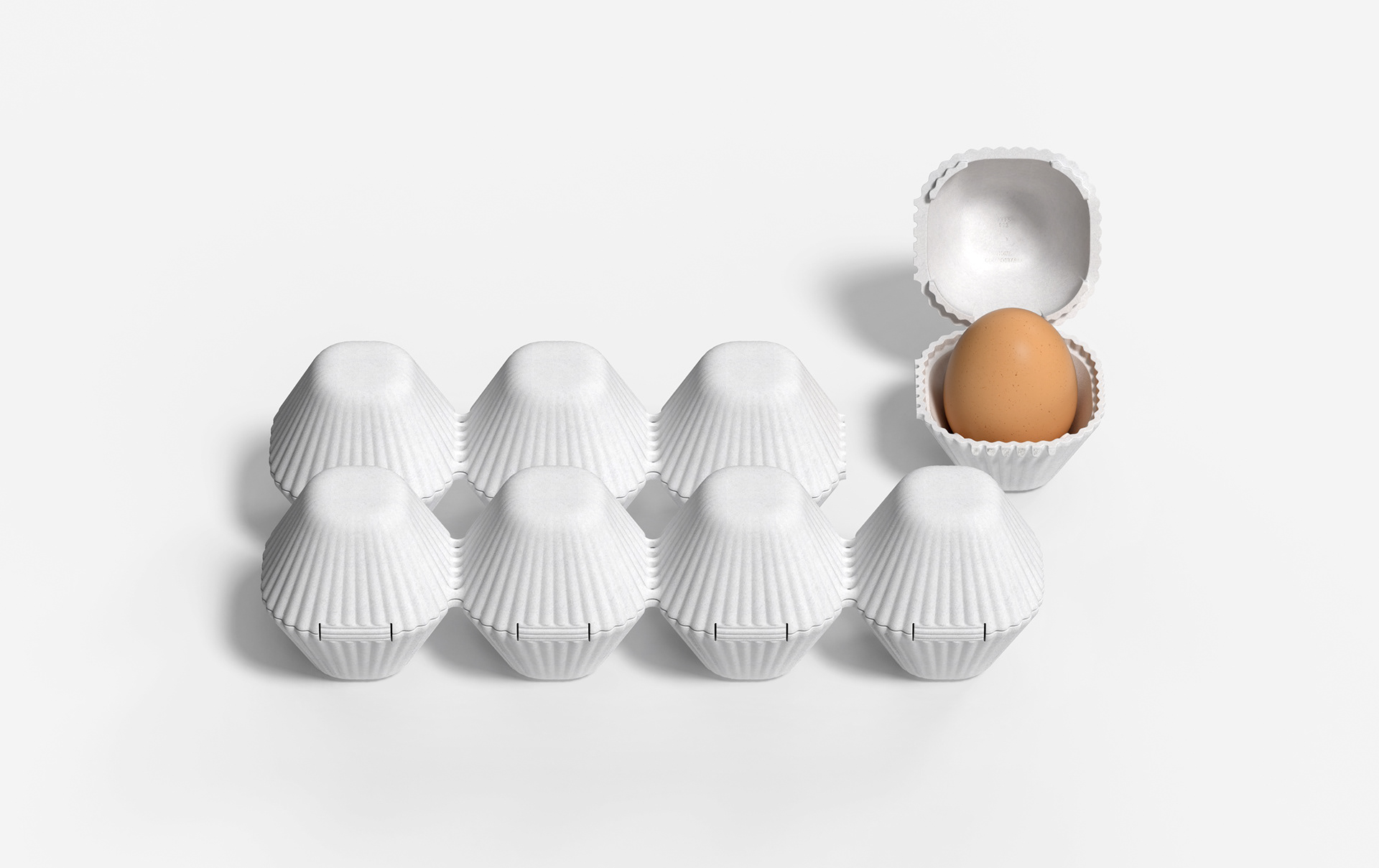
The Stamp Egg Package
made of PaperFoam®
The Stamp Egg Package is a detachable egg package made of PaperFoam® which is a sustainable, eco-friendly, low-carbon, highly recyclable, and home compostable material.
When you search for egg packages, you can easily find various shapes and methods to protect eggs. But all egg packages have fairly similar appearances because of their essential functions. The open and closed structure of the egg package must be suitable for the machine. In addition, they must have a structure to protect the eggs and be able to stack. As the design of the package needs to follow these rules, the shape of the package becomes similar.
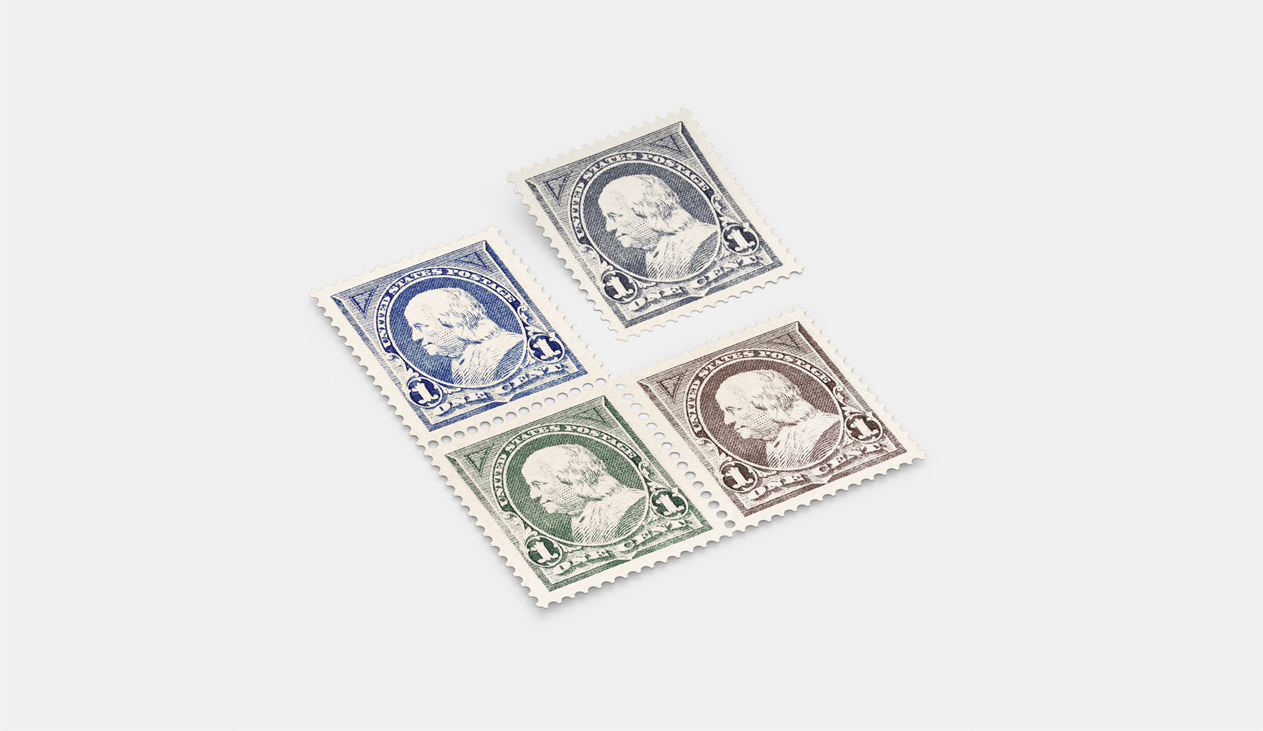
The Stamp is an egg package, which is inspired by a postage stamp, that follows these rules and even has the additional function of being able to separate individual packs. With this additional function, the users can save more space in the refrigerator and easily count the eggs without opening the package. Less opening and closing of the package means the eggs are less affected by the temperature changes, which keeps them fresher. Further, the separated egg package can be easily packed for a picnic or in a lunch box. With this additional feature of separation, this simple package gets to have more extended functions.
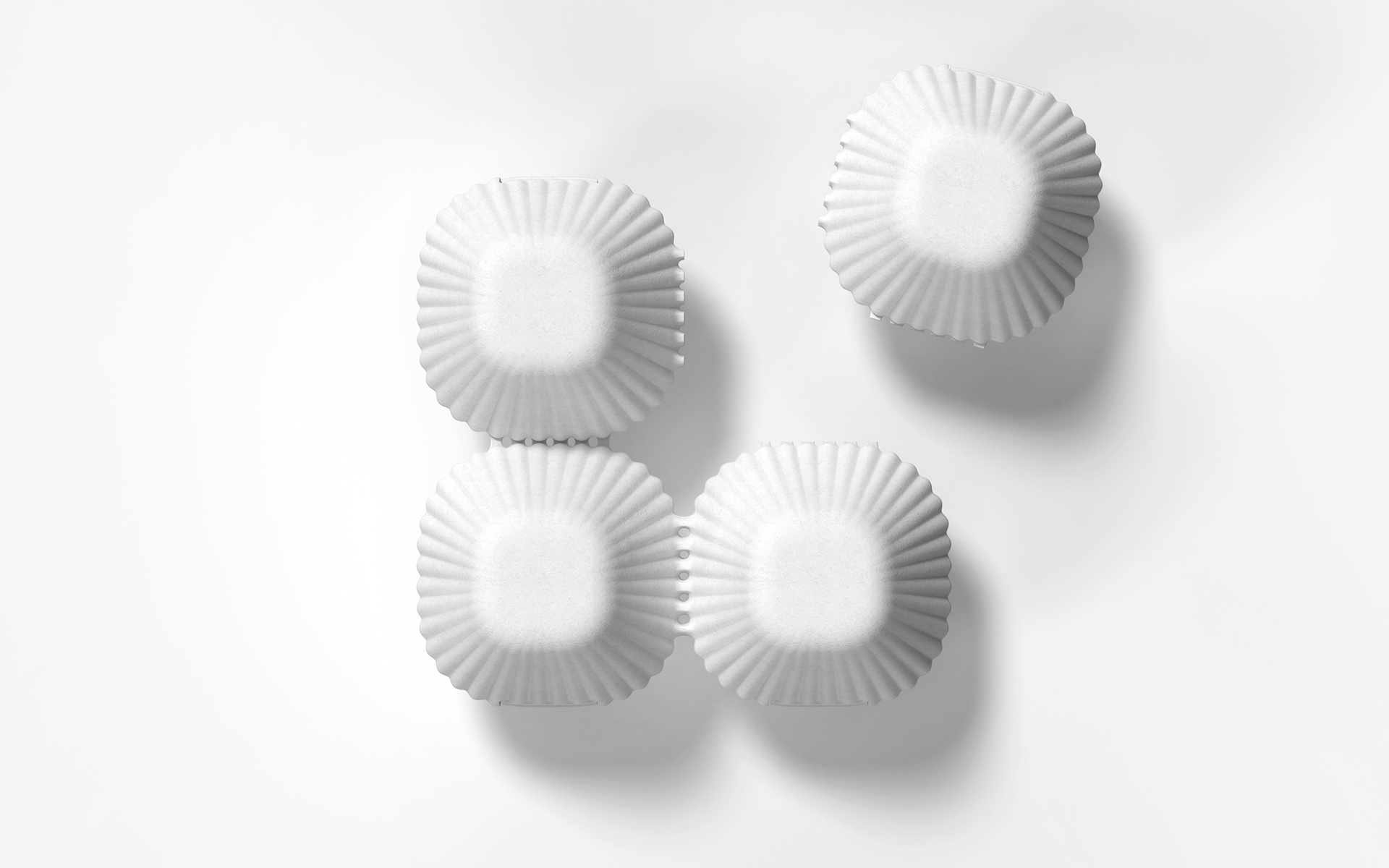
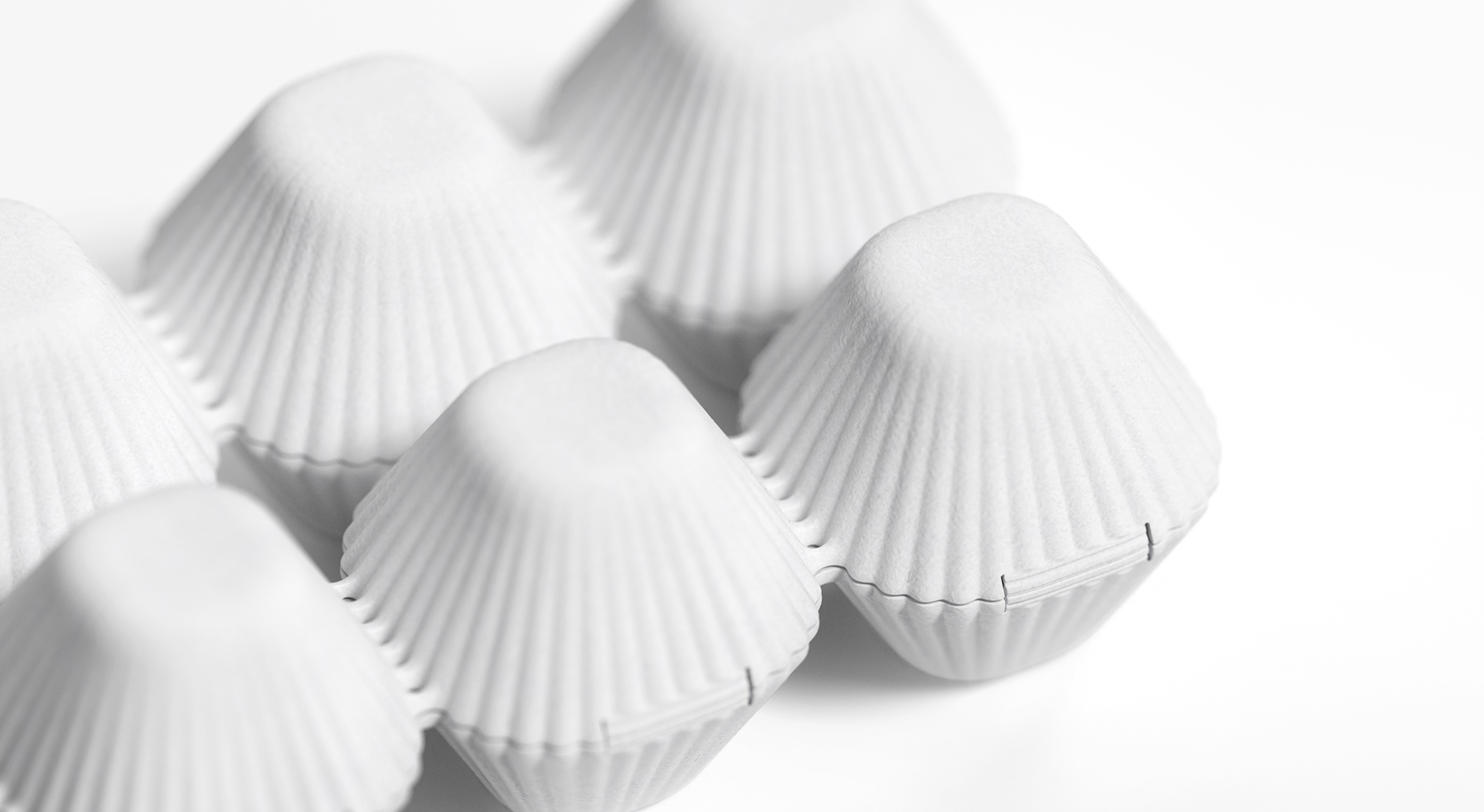
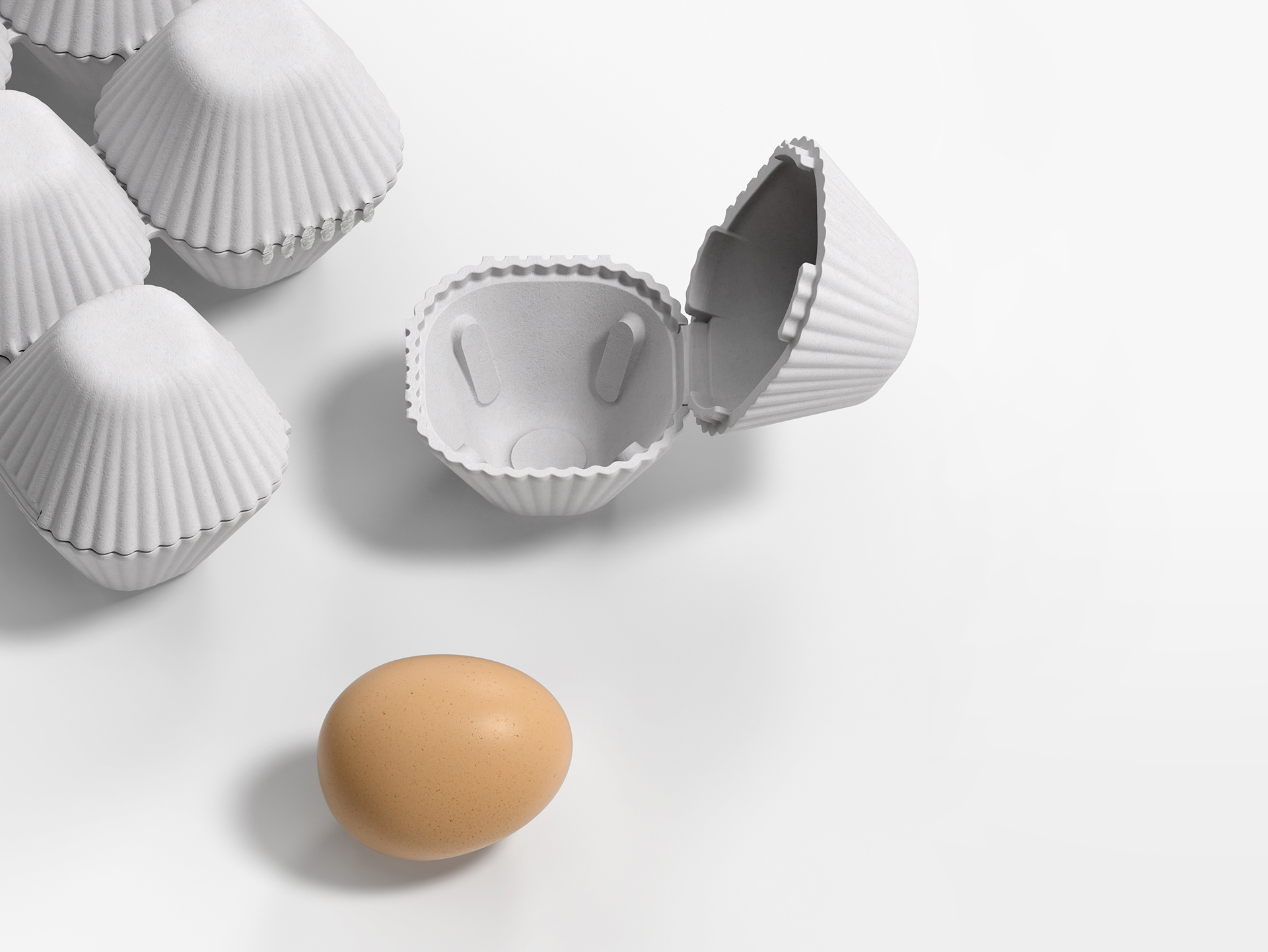
By providing better function and products through the use of eco-friendly materials, it is also a benefit that people use less plastic egg package and foam egg packages that cannot be recycled.
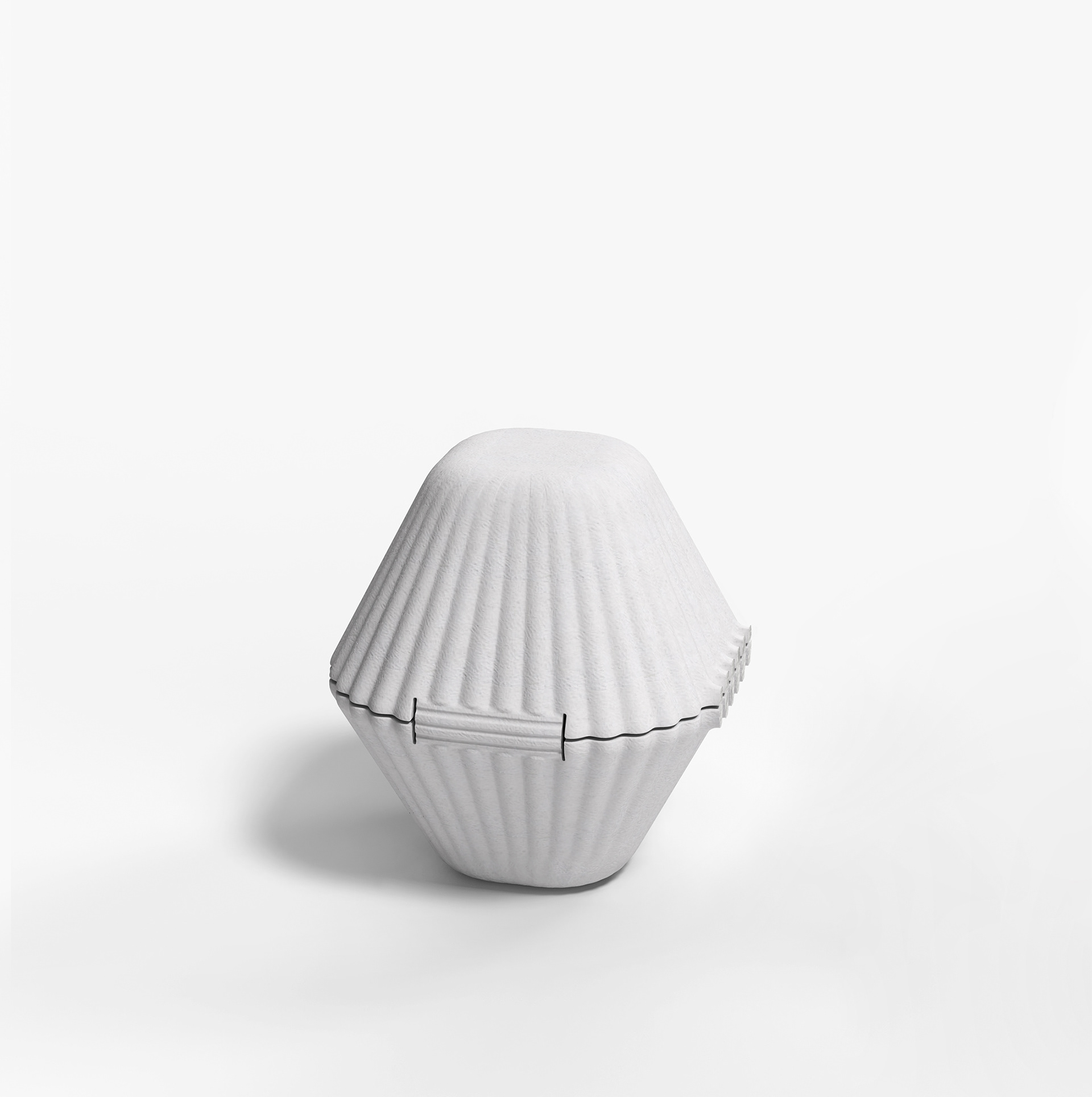
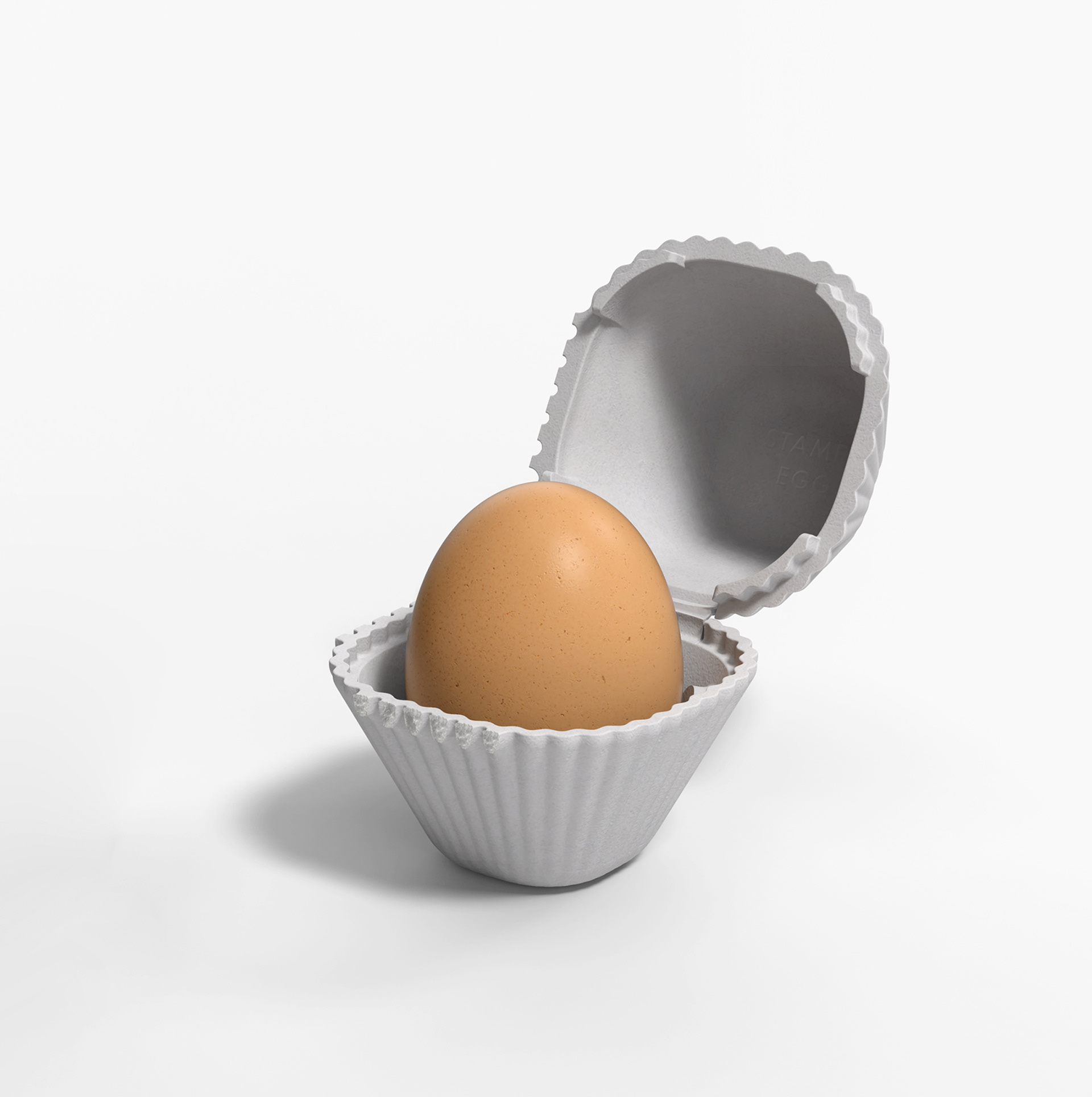
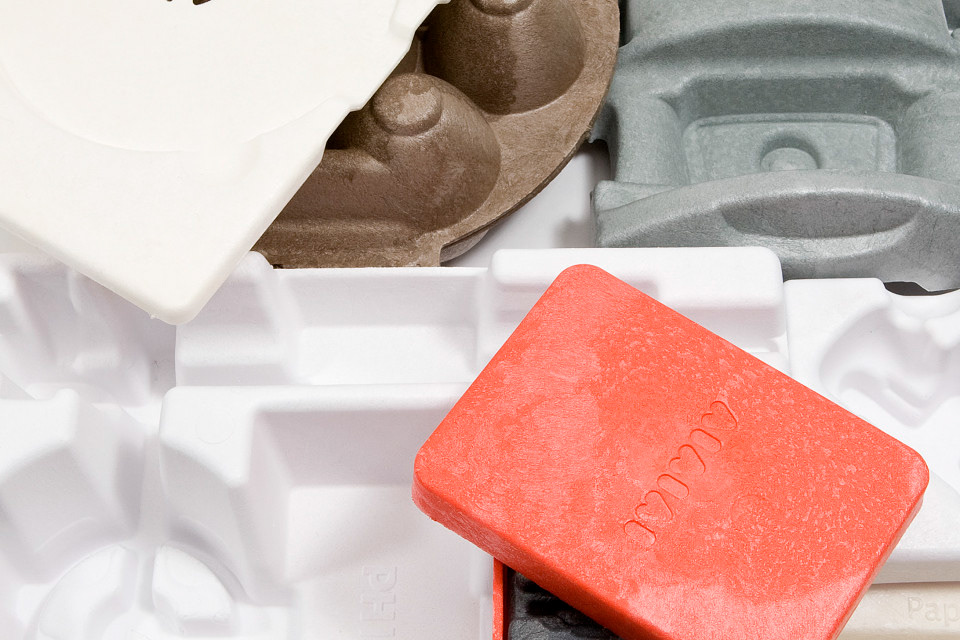
Material Investigation
PaperFoam, based in the Netherlands, is specialized in making environmentally friendly packaging material widely used in electronics, cosmetics, medical devices and food applications. Made out of starch, cellulose fibers and water, PaperFoam® is a bio-based product with a very low carbon footprint. In the waste phase, the products can be home composted or recycled with paper. Additionally, PaperFoam® is a CO2 saver insofar compared to similar molded pulps its mixture contains much less water, which causes a weight reduction of 40%. In the production phase, industrial starch, cellulose fibers, water and (where necessary) pigments, are blended for about 30 minutes until a slurry paste forms. The mixture is then injected into a mold, pressed and baked at 204 °C. The result is a light-weight, cushioning and nonabrasive material, available in a wide array of colors. Embossed and debossed details, textured surfaces, as well as clamping, hinging and closing mechanisms are easy to achieve. Featuring a maximum of three millimeters in thick- ness, PaperFoam® is a material which has not yet been used in any field other than packaging. I thus became interested in challenging the material to make Paper- Foam more resistant. I tried adding plant parts, such as leaves and petals, to the mixture of starch, natural fibers and water. I soon realized that the equipment and services I had access to within the educational environment did not allow me to achieve the sophisticated results I was looking for. Injection molding, in fact, requires a proper mold, an industrial press and correct baking time and temperature. I thus decided to focus on the design of patterns, playing with embossed and debossed details, textured surfaces and hinges. A well-thought-out industrially produced pattern can enhance the mechanical properties of the material as well as give an appealing aesthetic.
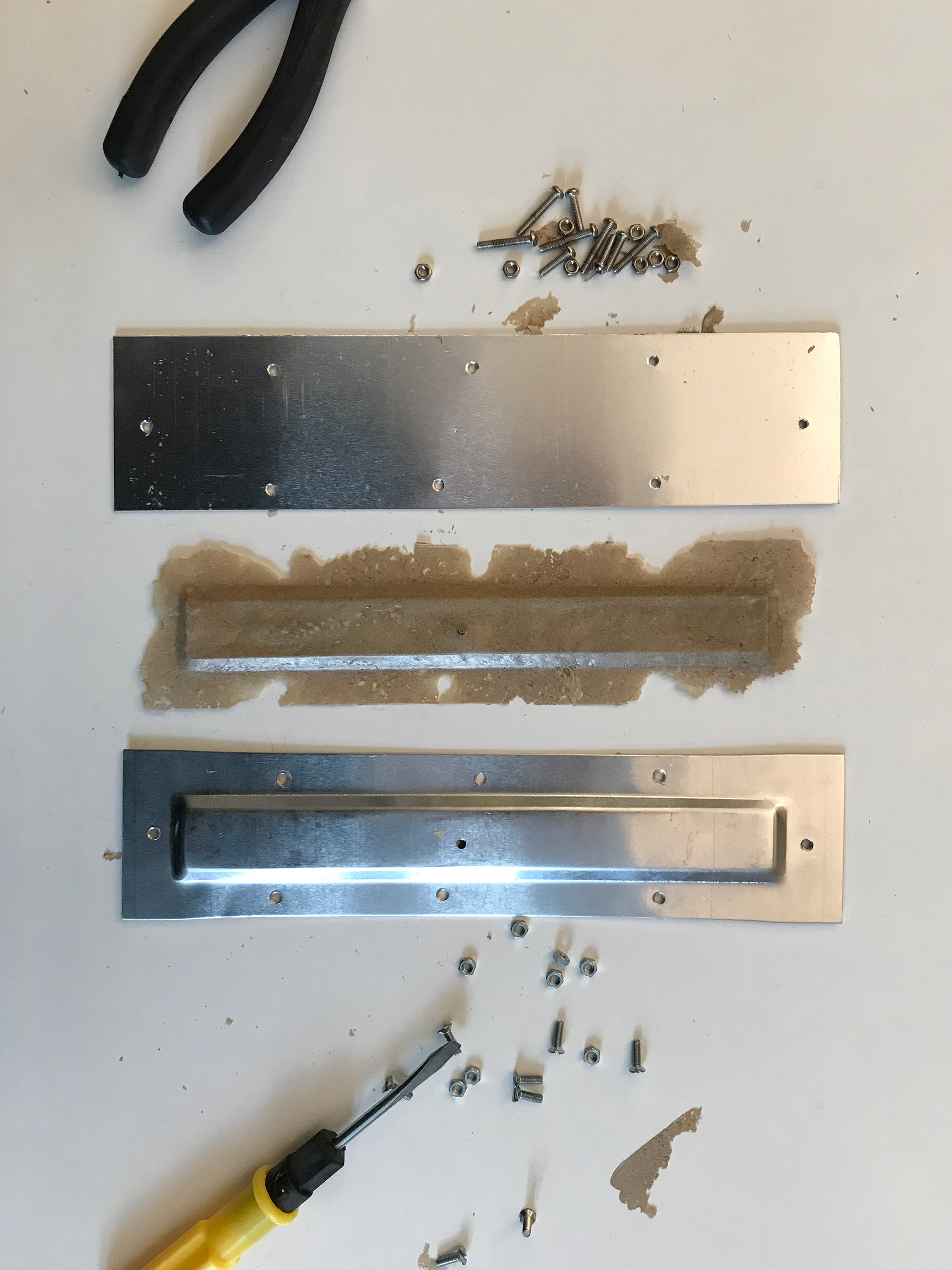
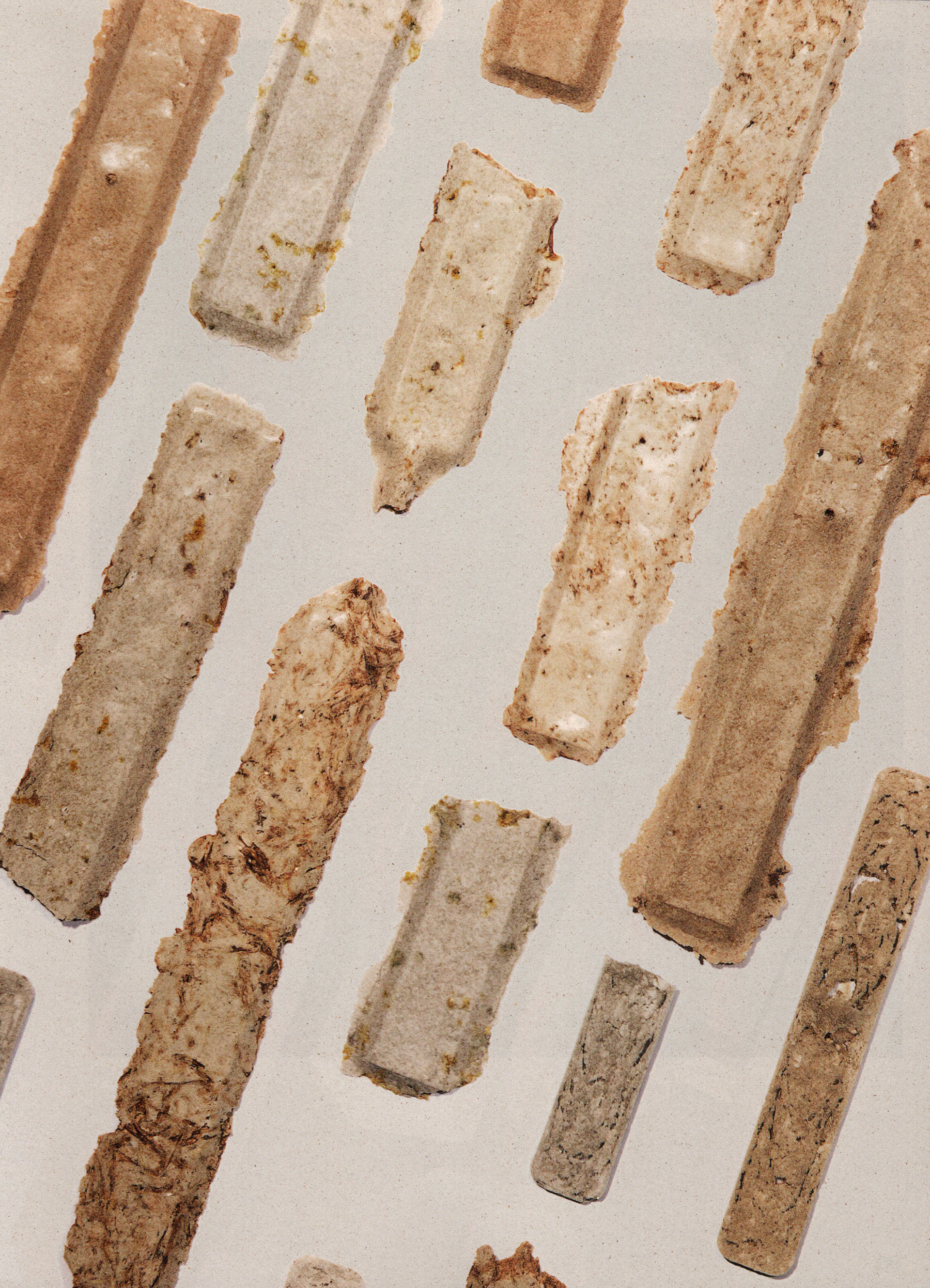
Intermediate Result
Because the versatility of moulding with injection moulds allows the design of sophisticated shapes, I designed an array of circle plates featuring double-sided patterns that act as samples. They feature a range of decorative embossed and engraved templates on one side and grooves on the other. It is important to reaffirm that the quality of finish achievable within a proper industrial environment would be far more sophisticated than the one l was able to achieve during my experimentation phase. These simple objects act as samples and show the different surface treatments and properties achievable by PaperFoam®, using the injection-molding procedure. These tests can then be easily adapted and tailored to specific objects for commercial purposes.
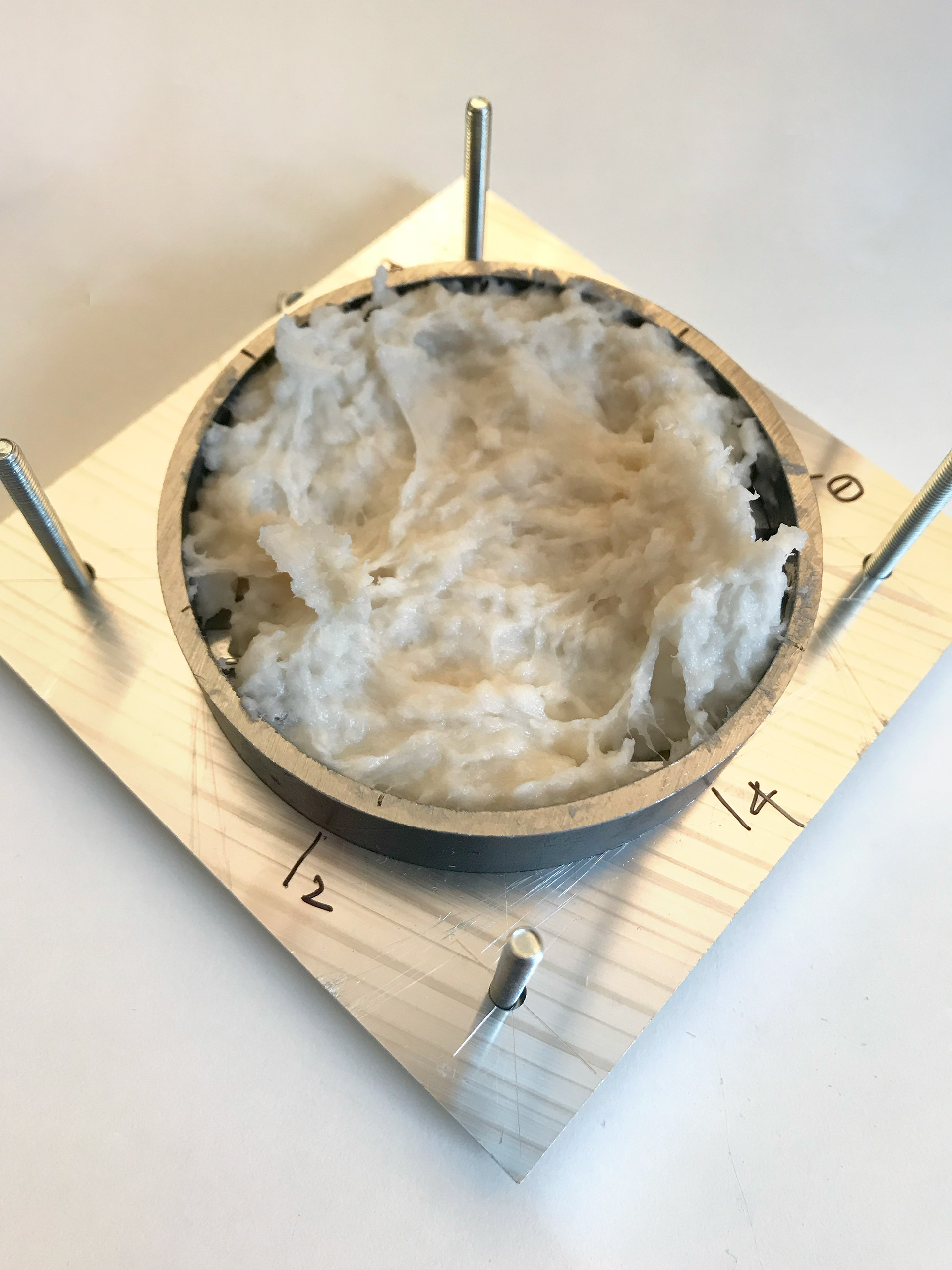
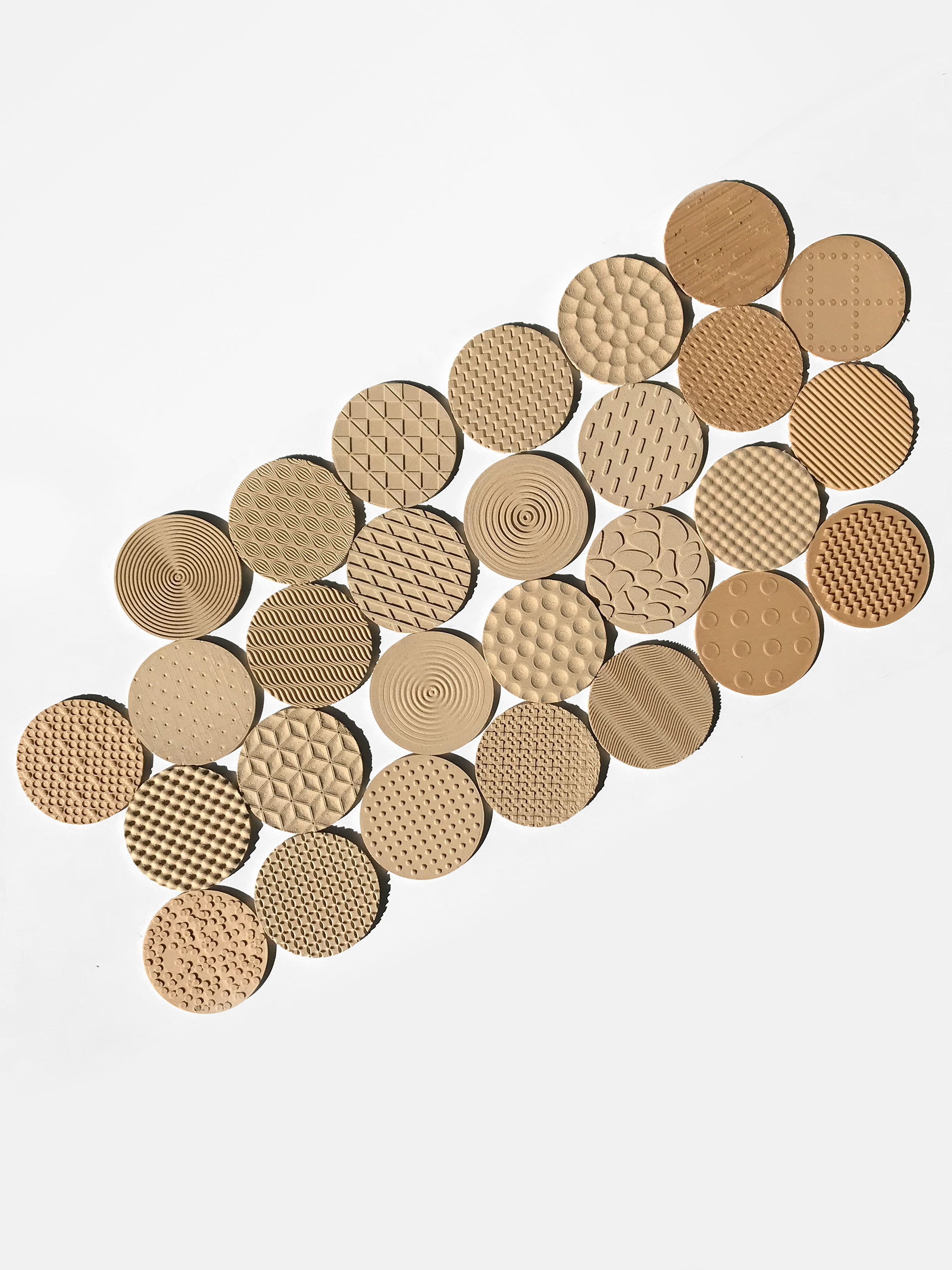
Product Development
After experimenting with the material to enhance its look and its mechanical properties, I had to find a prop- er application for my findings. I aimed at designing a mass-produced everyday object within the packaging industry, which proved to be a successful field of application for PaperFoam®.Among an array of possibilities, my interest focused on egg packaging. An egg box can be made out of various materials including polystyrene foam, clear plastic or moulded paper pulp by means of a mechanised papier-mâché process. New package designs and creative solutions are constantly being tested to replace the standard regular boxes. But none of these new products could really compete with the standard, cost-effective and high-performance boxes made of pressed paper. Hence, the challenge of approaching this project in a sustainable way, thinking about a valid and meaningful alternative to already existing products that would combine maximum efficiency with aesthetic quality using an environment-friendly approach throughout the whole lifecycle.
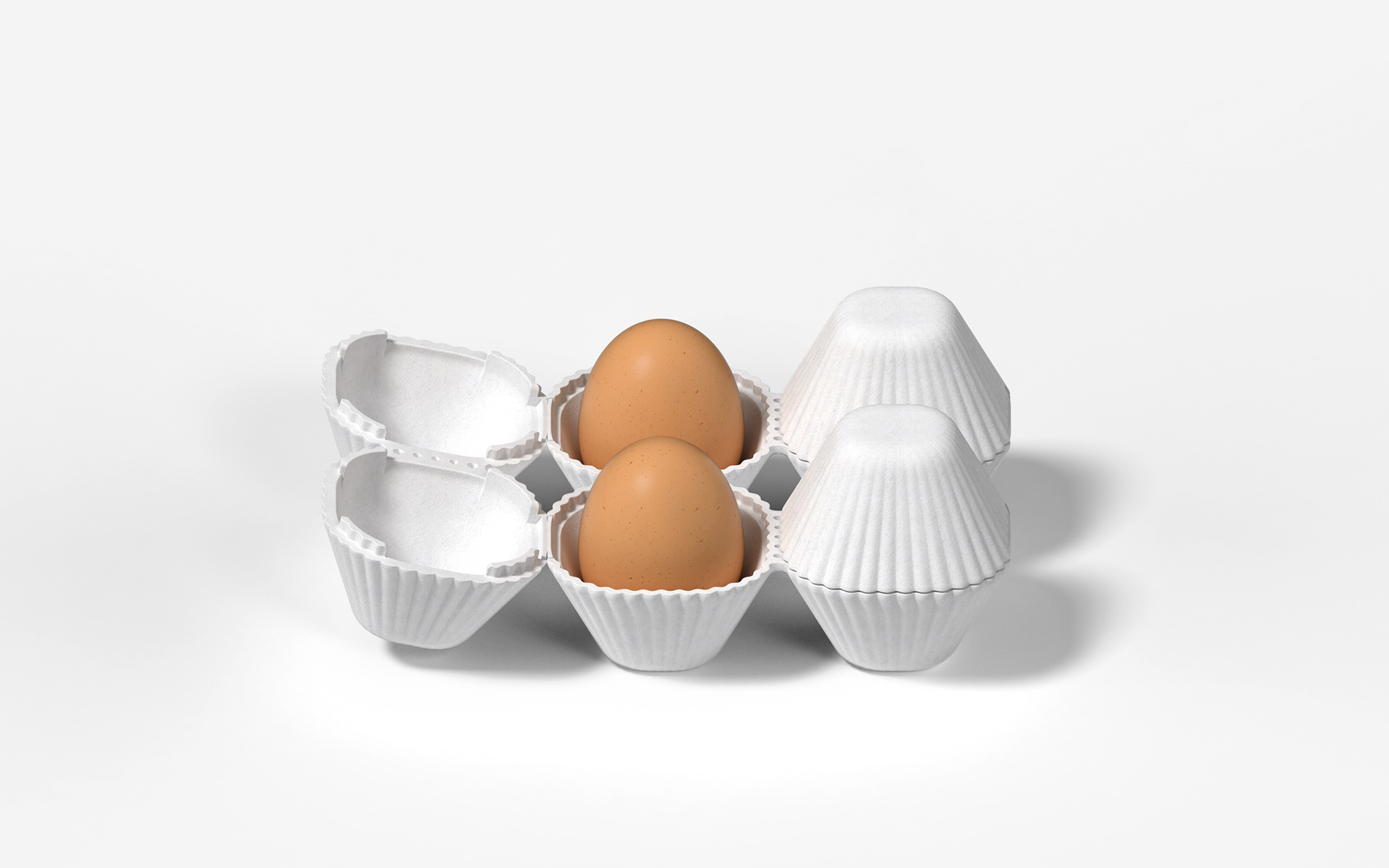
Final Outcome
Compared to the cellulose-pulp, foam or clear-plastic boxes, the PaperFoam® egg trays I designed are lighter (beaten only by the Polystyrene ones) and emit much less carbon dioxide compared to their competitors (96% less than pulp, 91% less than PS and 87% less than PET). They feature an appealing pleated outer shell that reinforces the PaperFoam® and helps to protect the eggs against stress exerted during transportation and storage. Easy to achieve with the injection-moulded manufacturing process, the outcome is a cost-effective, energy-efficient and attractive egg package. The cartons have dimpled forms to accommodate individual eggs and prevent them from coming into contact with one another. An improved hinge holds the units together and make the cups easy to separate into single independent boxes. With this additional function, the user can save space in the refrigerator and easily count how many eggs are left without opening the package. When eggs are not affected by temperature changes, their quality is proven to last longer. Moreover, the single units are easy to handle when going for a picnic or for a take-away meal. Like standard egg cartons, the PaperFoam® egg trays can come in a variety of colours and sizes, holding from three to twenty-four units. The name of the brand and the nutrient contents can be directly embossed on the material surface, saving on additional labelling costs. In the waste phase, the product can be home composted or recycled with paper.
isy studio.
Everything about the egg tray package, including projects of different materials, is in this book.
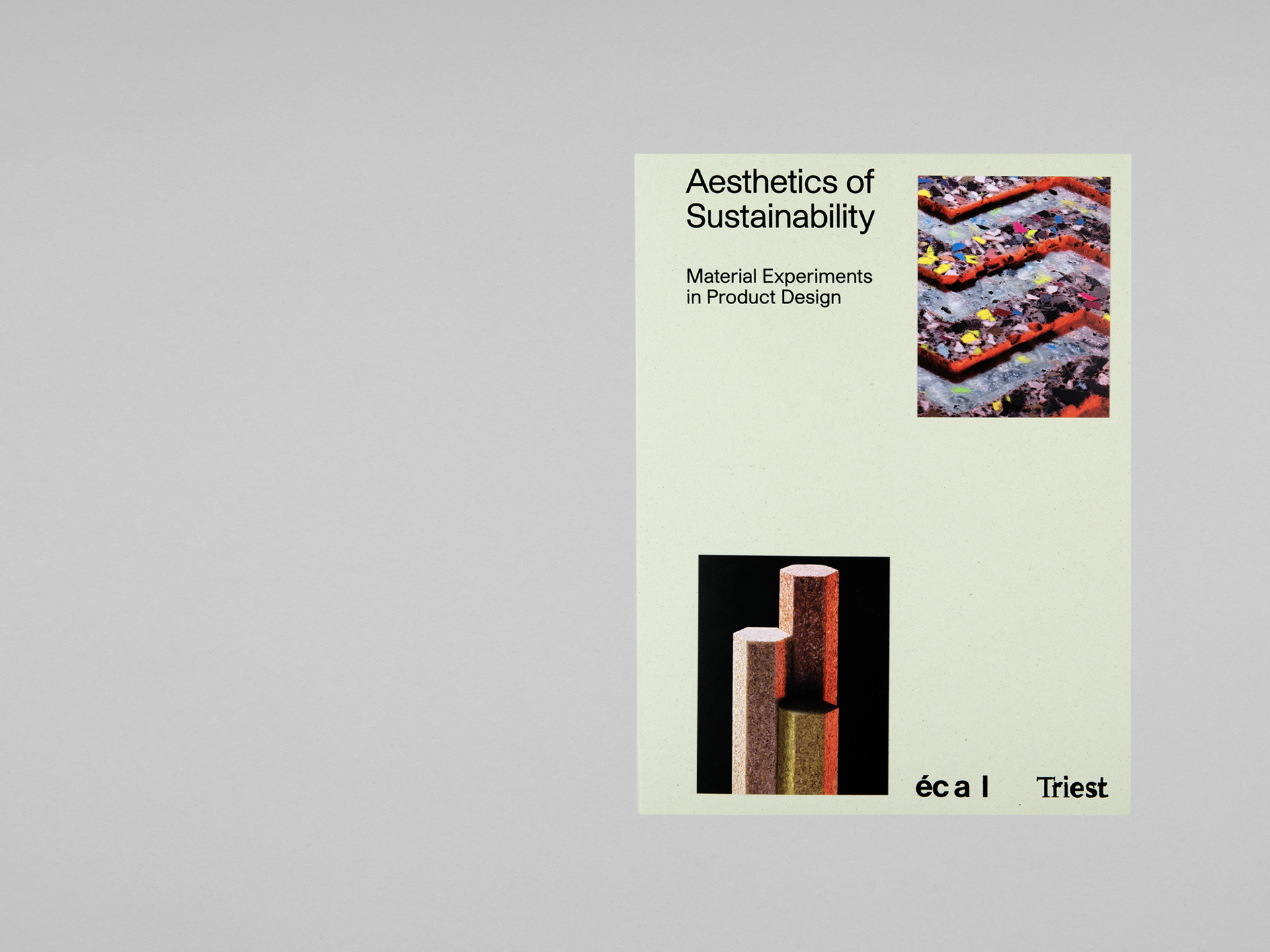
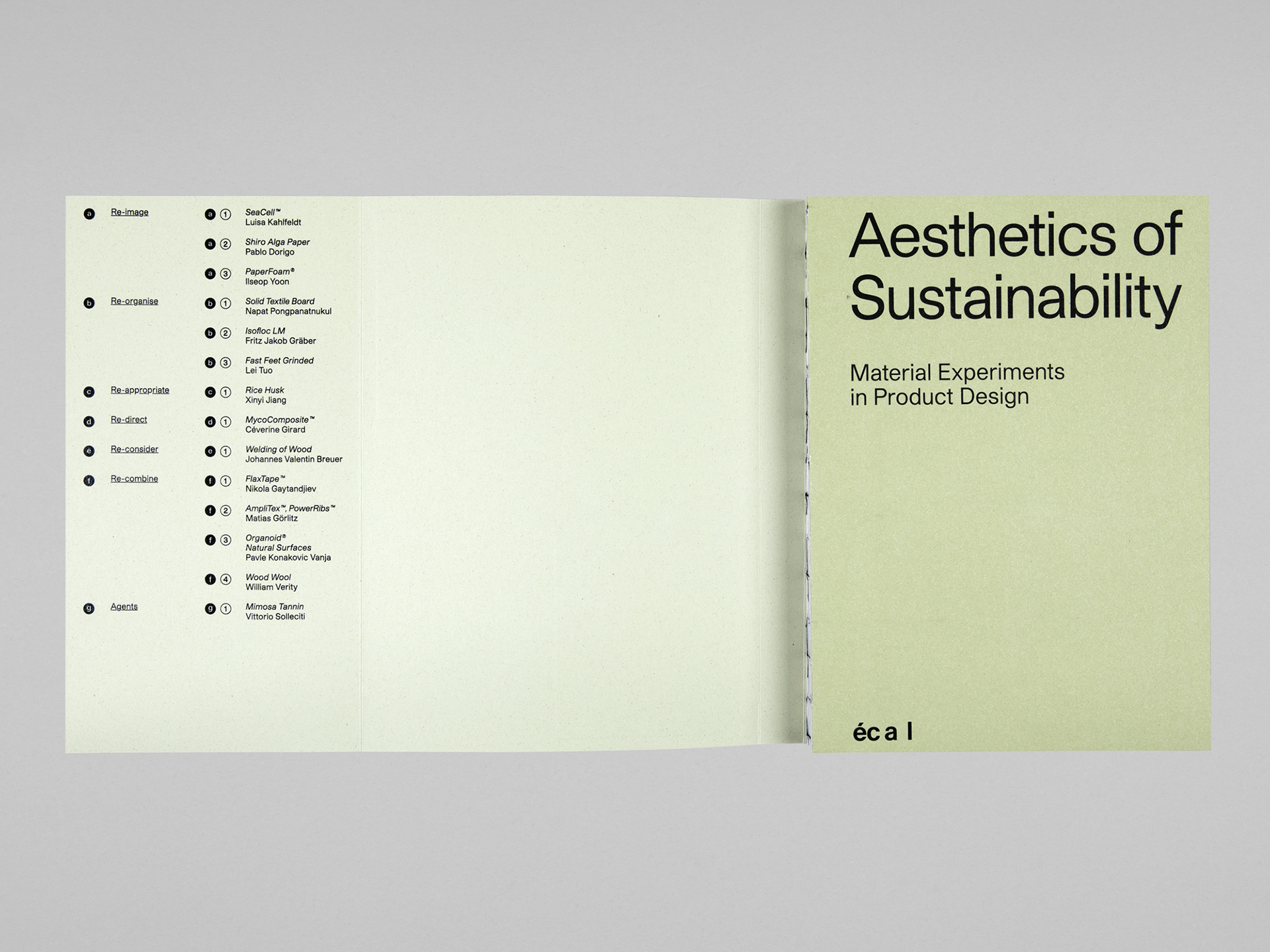
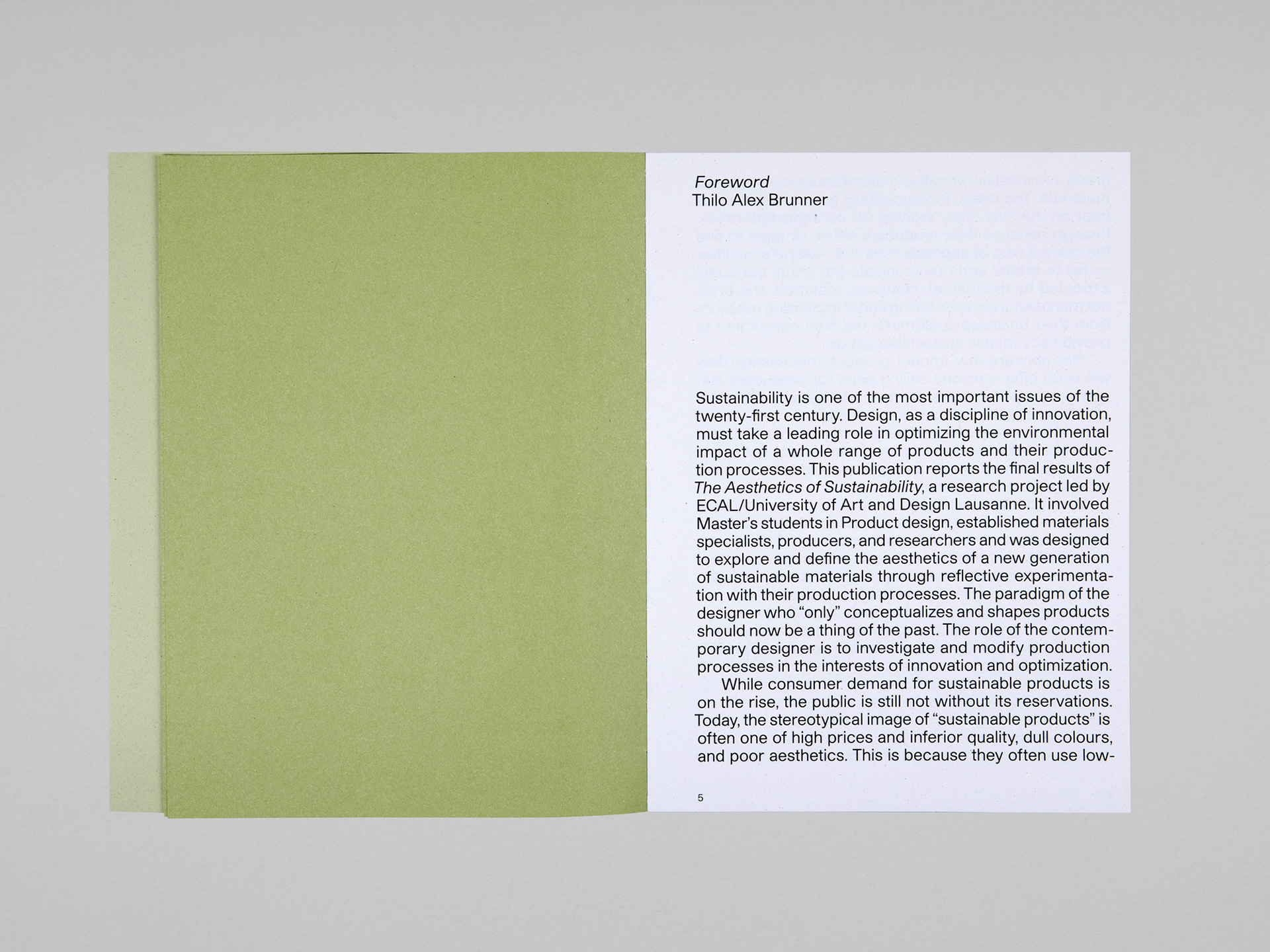
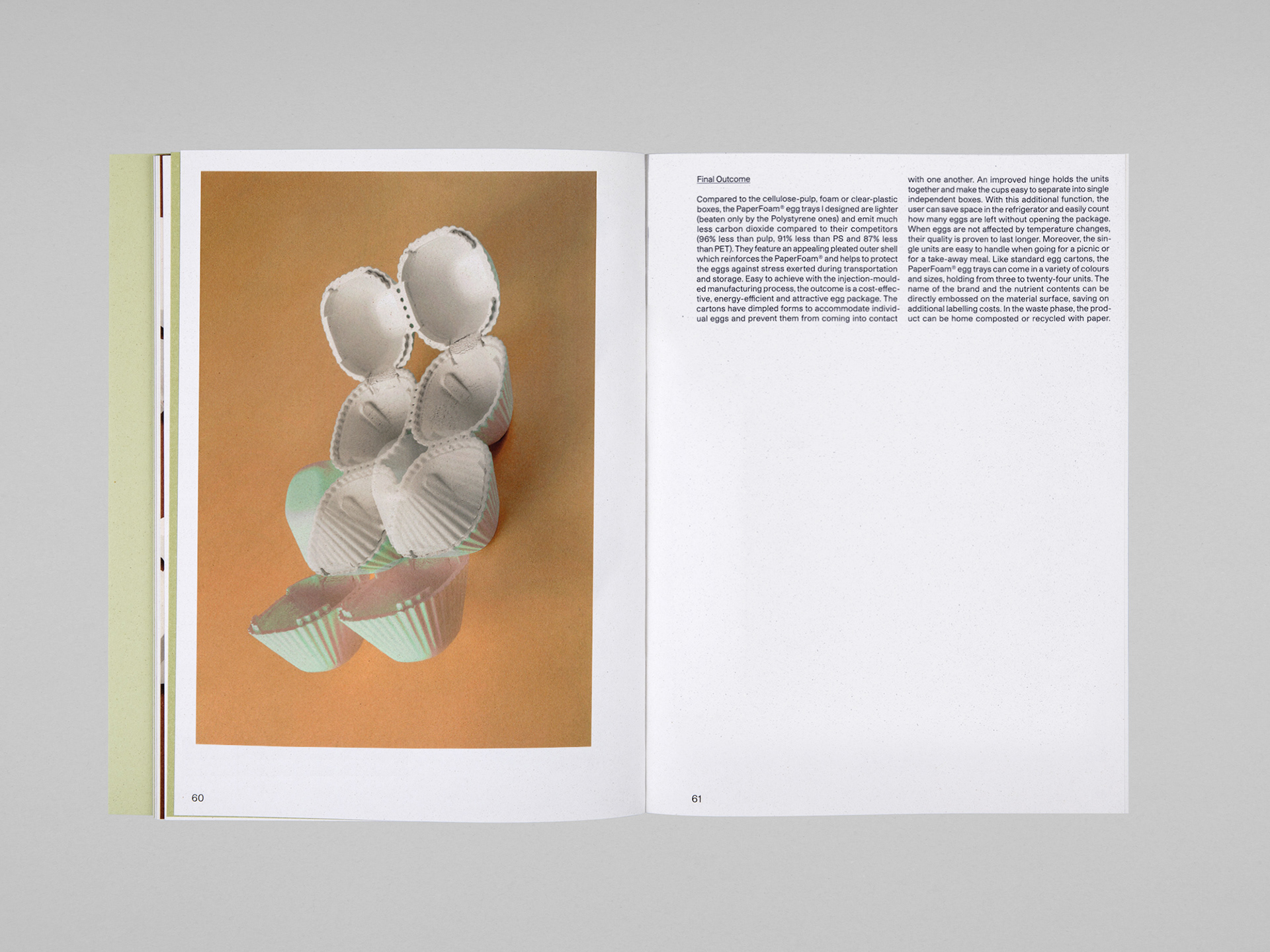
This book summarizes the results of “The Aesthetics of Sustainability”, a research project led by ECAL/Ecole cantonale d`art de Lausanne. It brought together Master’s students of Product Design, established materials specialists, manufacturers and researchers with the aim of exploring and defining the aesthetic potential of a new generation of sustainable materials. The result of this research-through-design project is a series of fourteen case studies involving the development of materials made from textile waste, recycled paper, rubber granulate or vegetable fibers such as algae, rice husks, hemp, flax and wood. The resulting new materials can be shaped, pressed, woven or welded. A selection of these materials will be presented through experiments and prototypes of products. The aim is to offer future designers a range of practical tools and applied knowledge about the methods of analyzing and processing seminal materials, utilizing their advantageous qualities and developing functional, yet aesthetically intriguing objects. The materials further aim to provide proof that sustainable materials are a great market opportunity for manufacturers and consumers alike.
https://ecal-shop.ch/en/product/aesthetics-of-sustainability/
https://ecal-shop.ch/en/product/aesthetics-of-sustainability/